DUMMY BLOCK
The dummy block transfers the pressure applied by the stem to the billet. A high tensile stress is therefore necessary. In addition, they are in direct contact with the hot billet during the extrusion process. The dummy blocks are thus locally subjected to very high temperatures. At the end of the extrusion process, the dummy blocks have to be cooled to the normal temperature. This results in high temperature fluctuations. In the case of extrusion with a shell there is also high hot wear at the edges.
The steels 1.2343 or 1.2344 with tensile strengths in the range 1500-1700 N/mm² suffice for light metals. The steel 1.2367 has proved itself for high stresses or fixed pad extrusion as it has a higher fatigue strength. Higher alloyed hot-working steels are necessary for heavy metals. Three dimensionally forged 1.2365 is usually used in the case of water-cooling. The working tensile strength is 1500-1700 N/mm². In the case of air-cooling, it is advisable to use the steels 1.2678 or 1.2889 with 1500-1700 N/mm², as they exhibit better hot wear resistance and temper resistance.
Steel 1.2888 has proved successful under higher stresses. Very good results have been obtained recently with an austenitic special steel (W512) with a similar basis to 1.2779. Increasing the Ti content results in significant increases in strength over 1.2779
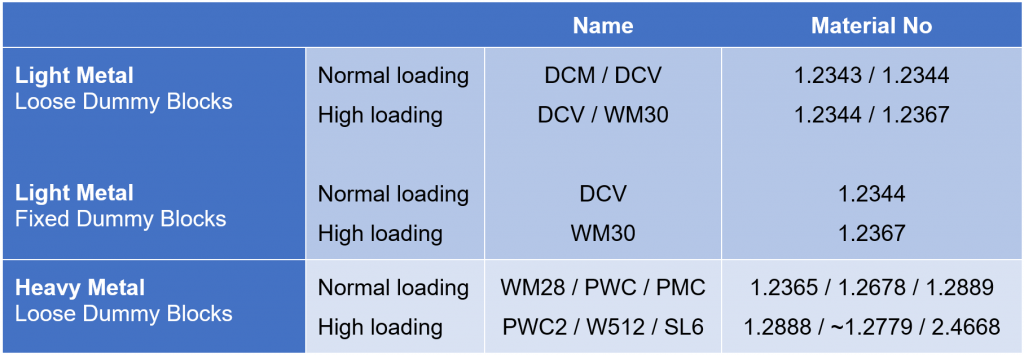
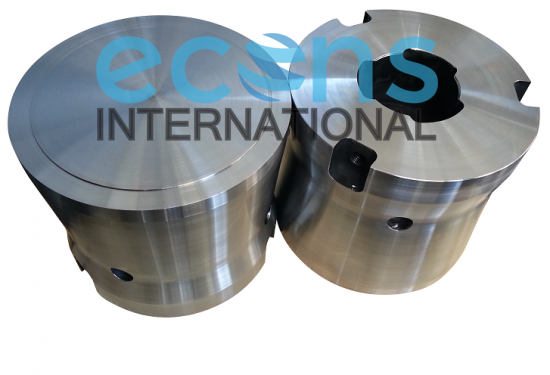
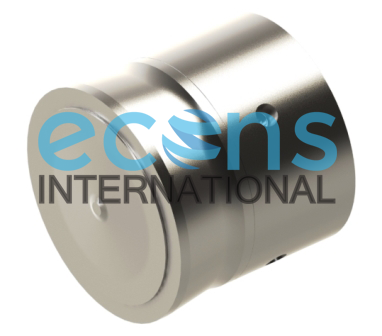
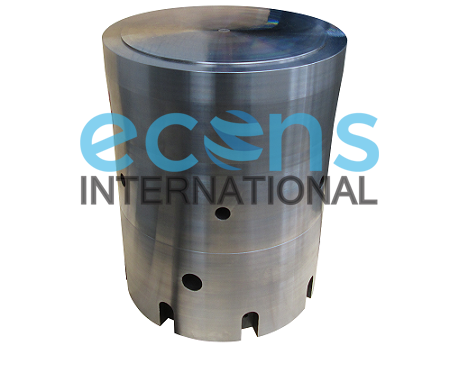